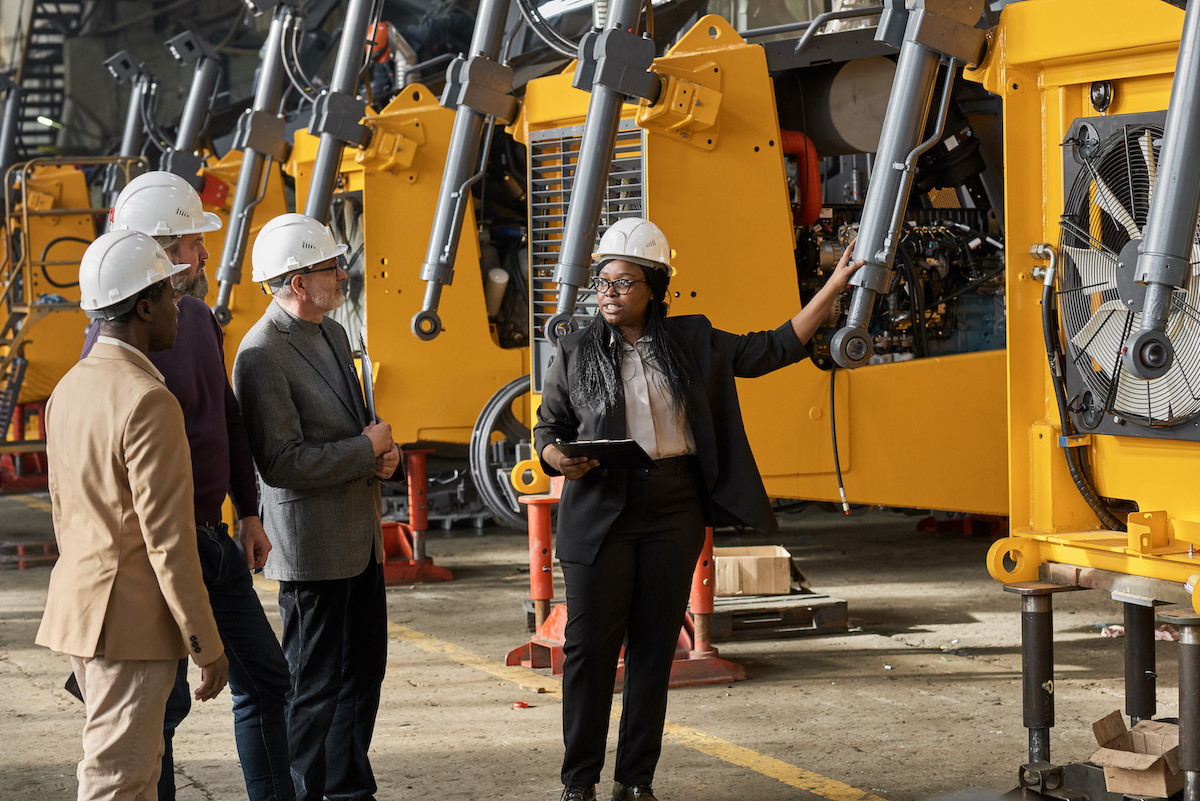
Have you thought about working with your supply chain partner on product design and assembly?
Address key factors such as the complexity and true life cycle cost of your product throughout the supply chain, sustainability and upgrade issues as part of design and development of your product and it impacts everything in a positive way from start-to-finish of the manufacturing and customer delivery process.
It makes no sense not to integrate the supply chain process with product design, so why don't manufacturers do it as a matter of course?
Product design and assembly can seem tough enough without involving others outside your core organisation. But it can be easy with a master supplier, 3PL/4PL, or full supply chain logistics partner, rather than corralling expertise and coordinating with a diverse network of suppliers (if you are still managing this through an overworked procurement department). A full spectrum supply chain partner should have the experience, vision and strategic overview necessary to collaborate with your procurement and design departments to create an effective product design/assembly strategy.
With 70-80% of product cost decided through the development and design stage of the product, areas of improvement further along the process and when production is up and running are limited without significant retooling or redesign costs. Adding a further layer of collaboration may increase complexity, but it offers the opportunity to create dividends in production flexibility, efficiency and financial value.
What is product design in the supply chain?
When the product development, manufacturing production, procurement (along with finance and marketing departments for full effectiveness) work together with supply chain partners to improve the quality, design and assembly of a product, it will reduce costs and lead to a step change improvement in value. It opens up a whole area of competitive advantage for the OEM.
Component sourcing, production complexity, warehousing and packaging, delivery and aftermarket care from the beginning to the end of the supply chain all impact on product design and supply chain costs. Inefficiencies can be eliminated and flexibility built into product creation, assembly and delivery if the product design and development process factors in supply chain constraints and opportunities from the start.
Key elements in the product design & assembly process
Collaboration in key areas can help with the challenge of creating the best product, assembled in the best way, and at the best price.
Component sourcing and sustainability
Price competitiveness is always a factor, but is the tip of the iceberg in terms of value and cost impact. Can the number of different parts be reduced? Can they be fewer of them? Is it the right calibre, quality and material? Where are the components sourced, from which countries, and what is the flexibility in supply? What is the supplier ability to dial up and down volume? These are essential questions to answer without even taking into account minimum order quantity, lead times, geopolitical unrest and shutdowns affecting component suppliers.
Transportation fluidity of parts and the time to transport, with the risk factors for delay and congestion, must be heeded with the need for greater resilience in the current global supply chain environment. Sustainability and ethical requirements have to be increasingly factored into manufacturer plans, with the ability to track these issues through provenance becoming greater factors.
Production complexity
More and differing components leads to increased supply chain complexity. What are the opportunities to rationalise the different types of components, and standardise through a family of products being manufactured by the OEM? Any improvements here lower costs, with reduced inventory complexity, de-risking of stock-outs, and the potential for mitigating supply reliance if managed correctly.
Besides standardisation and opportunities to use less custom componentry while de-risking supplier bottlenecks, less parts with reduced complexity should allow faster, simpler assembly and easier aftercare. Can modular design improve production line flexibility and efficiency? What types of fasteners are being used, and can screws and rivets be replaced by snap fits and adhesive parts?
Warehousing & packaging
Storage can be more easily standardised and managed, with efficient re-stocking and re-ordering amounts, along with appropriate buffer levels for resiliency and production activity needs as part of the bigger picture of component sourcing/management. Kitting and level of availability on-site are all part of orchestrating the production line based on design complexity and scheduling of assembly. Marrying these up makes the production process sing.
Packaging can be designed for efficient delivery of parts for assembly, as well as the best format for client post-assembly/delivery. Sustainability, cost, ease of assembly, fit-for-purpose material and environmental factors should all be factored in with forethought.
Delivery & aftermarket care
Delivery of materials needs to take into account transportation costs such as volume, weight, route time and freight issues by land, sea and air. What packaging and formatting of parts (ie. partial or full assembly with adequate protection and final site set-up and component kits to facilitate this at the client site) is necessary?
Consistency and durability in delivery and standardisation of components also ensures better aftermarket care, impacts product durability, and the ability to mend and upgrade effectively through the contract life of the product.
Putting it all together
Manage the product design process better, marry it with the supply chain in an active and thoughtful way and a company can mitigate supplier risks, demand-related risks, increase sustainability, and decrease a slew of other external risk factors. A cross-functional design process can lower costs by up to ~40% (Source: Bain & Company).
No easy playbook exists for implementing product design and assembly because many sectors are still operating with legacy business models and solutions that haven't been upgraded to take account of current global network opportunities and risks, along with a better understanding of digitisation and 4IR solutions to upgrade and integrate supply chain with the core manufacturing competencies.
Ready to find out more?
Experience and relevant expertise in the field is essential and something not accessible to management consultancies. Acorn have the real-world supply chain and logistics experience to help, learn more about our product design & assembly service here.