We offer precision machined components for your assembly line needs. Both CNC turning and CNC Milling for creation of precision machined components are available as part of our precision machining service, with the capability of fabricating simple and complex parts, made to drawing, from 2mm dia to 250mm dia.
As a leading components distributor, we can supply precision machined parts direct to line via a multitude of ordering systems, including VMI, Kanban and DLF (direct line feed).
We know that assembly in OEM manufacturing requires accurate tolerances, high quality materials, and precise assembly. Precision machining methods are perfect for this: providing high replicability and accuracy, less material waste and defects, and consistent sourcing.
We recognise that having reliable, high quality component supply is critical for industries such as aerospace and medical sectors. Over- or under-stocking creates inefficiencies with assembly time and capital cost. Acorn are experts at providing the right stock at the right time for your assembly line.
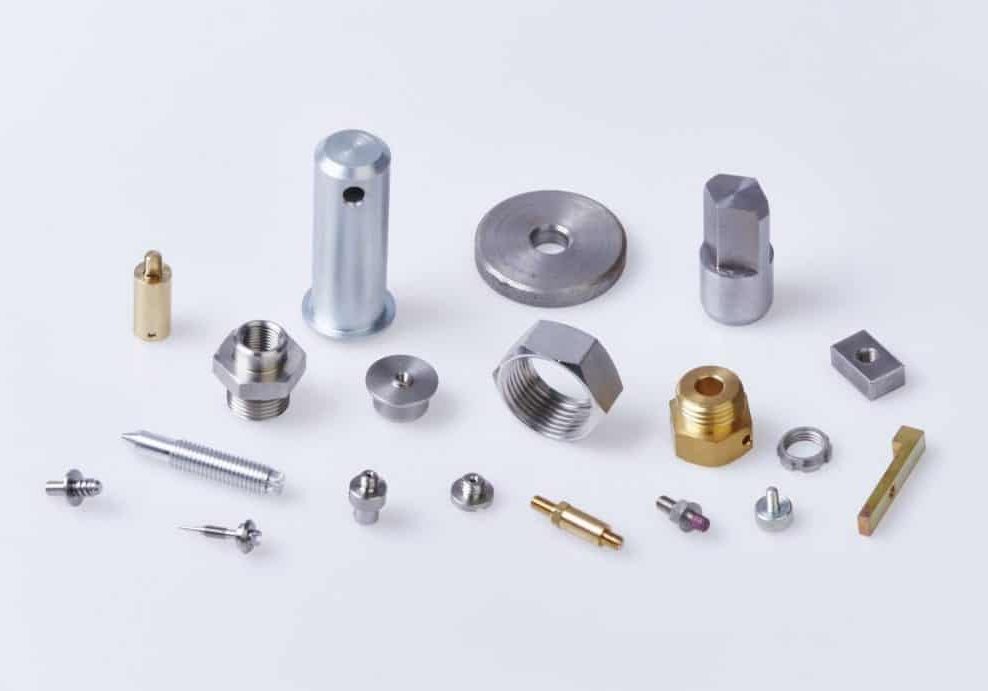
Precision machined components: examples
We can provide components made from the following materials: steel, stainless steel, aluminium, brass, nylon and almost all exotic materials.
Design for precision machining
In our experience these design strategies can help you focus on sourcing the best custom precision components within OEM applications and manufacture.
Simplify Your Assembly Process
When designing your component, consider the assembly process along with any post-production steps. Aim for easily accessible surfaces and fasteners that are straightforward to reach. This not only aids in the manufacturing process but it also contributes to more efficient assembly lines. How can you reduce steps and simplify assembly for speed and continued maintenance?
Opt for Precise Tolerances
Balancing precision and practicality is key for value and quality markers. To achieve mission-critical accuracy, specify tight tolerances for your components. However, be conscious that tighter tolerances can impact both the cost and lead time. What is the tolerance band appropriate to your application?
Streamline Component Complexity
Intricate parts require advanced machining techniques and more time for production. Where possible, opt for smooth and uniform surfaces, with minimal additional features. This approach usually results in both time and cost savings. Simpler surfaces require less machining and are likely have higher uniformity.
Leverage Standard Features
Incorporating standard features like threaded holes can significantly reduce both the lead time and cost. This is a simple yet effective way to streamline the production process without sacrificing quality. What standard components and features can be incorporated into design/assembly?
Plan for the Final Finish
If you're considering coatings or other finishing processes, design your part accordingly. You may need to leave additional material on the component to achieve the desired final finish.
Types of precision machining equipment
These methods encompass the range of options for part design and manufacturing. Each has speific advantages and limitations in terms of cost, complexity, and lead time. Leverage our expertise to get the best components using the best of these equipment types.
Multi-axis CNC — A comprehensive system allowing movement over four or more directions for complex parts creation. Synthesises milling, waterjet, and laser cutting into one machining process flow.
CNC Milling — Offers versatility in removing material for final component form with variable direction, angle, and speed. Comes in various forms like C-frame and gantry, catering to diverse needs.
CNC Turning — Involves a rotating workpiece and a linear cutting tool, primarily using single-point tools. Ideal for streamlined, cylindrical components.
CNC Drill Presses — Stationary workpieces meet rotating drill bits, creating holes for assembly or appearance. Hole size and depth are highly controllable.
Precision Grinders — Finalises manufacturing by creating flat, smooth surfaces. Employed for close-tolerance finishes, removing minuscule amounts of excess material.
Electrical Discharge Machining (EDM) — Specialised for hard metals, it employs electrical discharges to shape materials through melting. Commonly used for intricate features like gearing slots, holes and tapers.
CNC Laser Machines — Uses laser beams for slicing or engraving, applicable to both metals and non-metals.
Get precision machined components with vendor managed inventory
Acorn specialise in solving logistics headaches, and improving the supply chain logistics for OEMs.
Learn more about how a managed inventory system can help you with supplying your precision component needs